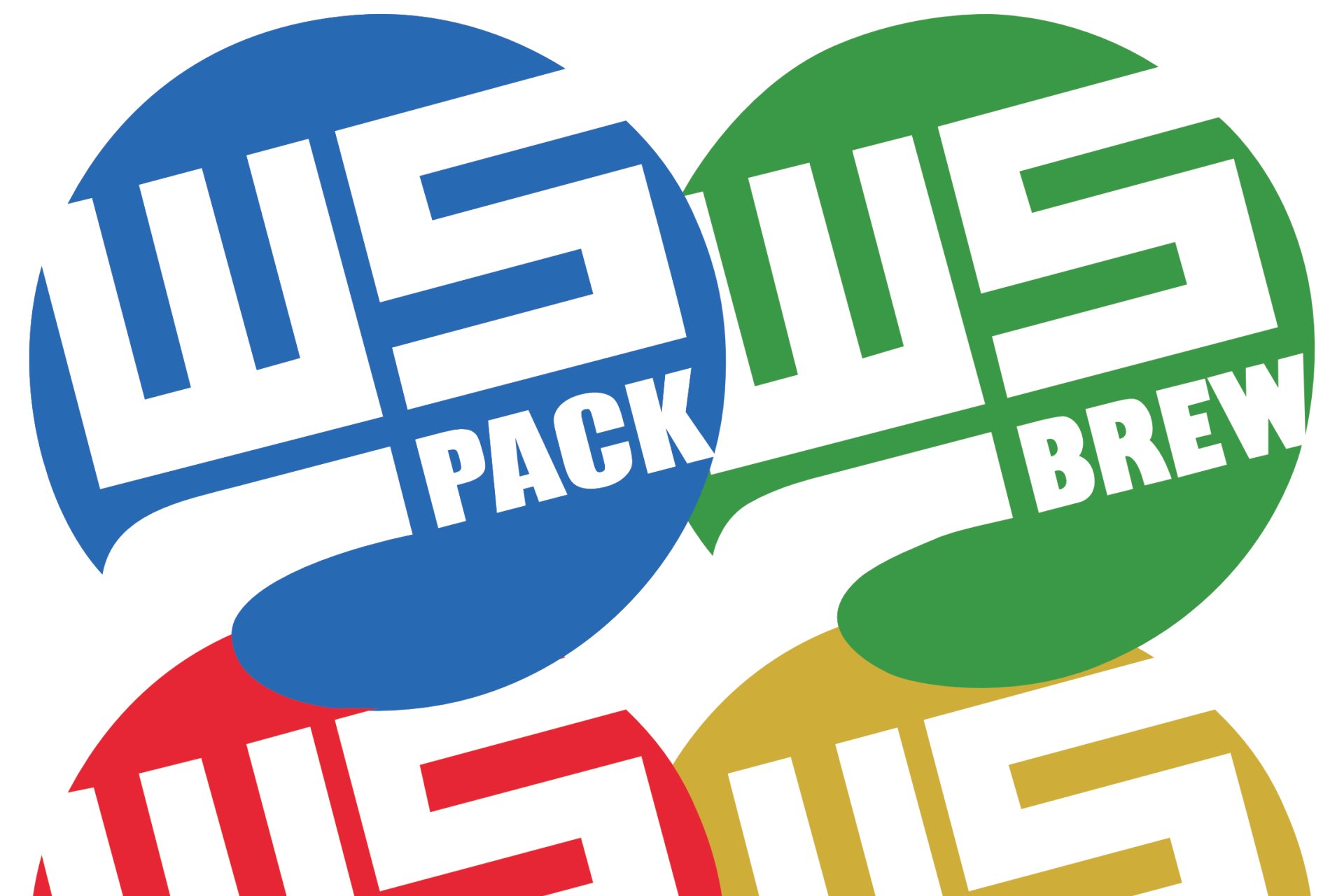
Autor | Institution |
---|---|
Raik Bär | Lehrstuhl für Lebensmittelverpackungstechnik, TUM |
Datum | 14. August 2019 |
Ausgabe | 3 |
Jahrgang | 87 |
Seitenzahl | 116-118 |
Digitalisierung, Maschinen- und IT-Vernetzung, MES, ERP... seit einigen Jahren bestimmen diese Begriffe die Industrie. Insbesondere die Nahrungsmittel- und Getränkeindustrie befasst sich intensiv mit diesen Themen, da sie besonders gefordert ist, qualitativ hochwertige Produkte zu marktgerechten Preisen anzubieten.
Um die Wettbewerbsfähigkeit zu erhalten, sind Produktionsbetriebe auf eine effektive informationstechnische Unterstützung der innerbetrieblichen Prozesse angewiesen und setzen daher vermehrt auf den Einsatz prozessnah operierender Fertigungsmanagementsysteme, sogenannte Manufacturing Execution Systeme (MES). Die Implementierung dieser Systeme ist meist mit zeitaufwendigen Schnittstellendefinitionen und dadurch mit hohen Kosten verbunden. An diesem Punkt knüpfen die Weihenstephaner Standards (WS) an. Was im Jahr 2000 als „Standard-Pflichtenheft für BDE-Systeme innerhalb von Getränkeabfülllinien“ begann, hat sich als „WS Pack“ im Flaschenkeller mittlerweile als internationaler Standard durchgesetzt. Vergleichbare Standardlösungen im Prozessbereich der Brauerei fehlten bisher. Projekte wurden jeweils individuell umgesetzt.
In einer Laufzeit von zweieinhalb Jahren wurde daher der neue Standard „Weihenstephaner Standards für Brauereiprozesse“ (WS Brew) in einem großen Projektkonsortium erarbeitet und mittlerweile veröffentlicht.
Dieser Beitrag geht kurz auf die Weihenstephaner Standards im Allgemeinen ein, um im Anschluss die neueste Ausweitung der WS im Brauereiprozessbereich zu beleuchten. Bereits in „Der Weihenstephaner“ Ausgabe 3/2017 wurde u.a. vom Anstoß des Projektes „Weihenstephaner Standards für Brauereiprozesse“ berichtet.
Standardisierte Schnittstellen zur Anlagenkommunikation
Grundsätzlich bieten die Weihenstephaner Standards eine standardisierte Schnittstelle hinsichtlich Inhalt und Kommunikation zwischen Anlagen bzw. Maschinen und übergeordneten IT-Systemen. Bisher definiert die physikalische Schnittstelle zum einen das Netzwerk (Ethernet TCP/IP) und zum anderen das Protokoll für das Verbinden von Maschinen und Kontrollgeräten mit einem MES oder Datenerfassungssystem. Der inhaltliche Teil der Schnittstelle ist durch branchenspezifische (OMAC-konforme) Dateninhalte definiert. Im Fall der obligatorischen Datenpunkte müssen diese von den Maschinen einer Produktionsanlage bereitgestellt werden. Optionale Datenpunkte definieren jene Inhalte, die zusätzlich angeboten werden können. Zudem sind in den bisherigen Weihenstephaner Standards Auswerteempfehlungen beinhaltet, welche die notwendigen MES-Funktionen der Lebensmittel- und Getränkeindustrie beschreiben. Darin wird aufgezeigt, wie eine lückenlose Chargenrückverfolgung ermöglicht, Kennzahlen berechnet oder entsprechende Produktionsberichte anhand der bereitgestellten Datenpunkte erstellt werden können.
Zusätzlich wurden zur Unterstützung bei der Implementierung der WS zwei Softwaretools in Zusammenarbeit mit Projektpartnern des Industrieanwenderkreises (Arbeitsgruppe bestehend aus Unternehmen mit einer WS-Firmenlizenz) entwickelt. Das „WS Testtool“ kann zur Überprüfung der Schnittstelle verwendet werden, wohingegen das Tool „WS Edit“ die weitgehend automatisierte Erstellung der XML-Gerätebeschreibungsdatei ermöglicht, die den Dateninhalt, den die Maschine anbieten soll, definiert. Die vorgefertigten branchenspezifischen Datenpunktbibliotheken (WS Pack für die Verpackungsindustrie, WS Food für die fleischverarbeitende Industrie, WS Bake für die Bäckereiindustrie) beinhalten alle obligatorischen und optionalen Datenpunkte. Darüber hinaus können noch weitere kundenspezifische Datenpunkte festgelegt werden.
WS Brew
Angestoßen wurde das Projekt Weihenstephaner Standards für Brauereiprozesse ebenfalls aus dem Industrieanwenderkreis. Vertreter großer und mittelständischer Brauereien, Anlagenbauer und IT-Systemanbieter forderten MES-Schnittstellen-Standards für die prozessseitige Bierproduktion (Malzannahme bis Drucktankkeller).
Die Ausgangslage hierfür waren Erfahrungen innerhalb von Projekten, in denen die Kommunikation zwischen Kunden und Anbietern schwierig war und stets erheblicher Diskussionsbedarf bestand. Durch maßgeschneiderte, individuelle Lösungen, welche sich nur schwer auf andere Betriebe übertragen lassen, fallen die Projektkosten meist höher aus als geplant. Daher wurde der Lehrstuhl für Lebensmittelverpackungstechnik beauftragt einen entsprechenden Projektplan auszuarbeiten, um die Anforderungen und Bedürfnisse der beteiligen Projektpartner zu bestimmen und die umfassenden Standarddefinitionen zu erarbeiten. Projektziel von WS Brew war demnach die Definition der Schnittstelle zwischen Anlagen bzw. Leitsystem und MES in Bezug auf Dateninhalte und Semantik, basierend auf dem etablierten WS-Konzept. Berücksichtigt werden sollten hierbei die wichtigsten Prozessbereiche der Brauerei: das Sudhaus, der Gär- und Lagerkeller, die Filtration und die verbundenen Betriebseinrichtungen, wie z.B. die Dampf- oder Drucklufterzeugung.
Mit den Standarddefinitionen wird ermöglicht, alle notwendigen MES-Funktionen ohne Schnittstellenprobleme zu implementieren. Der erarbeitete Projektplan umfasste dabei folgende Arbeitspakete:
- AP1: Anforderungsdefinition;
- AP2: Bestimmung der brauereirelevanten MES-Funktionalitäten;
- AP3: MES-Funktionsbeschreibung und -modellierung;
- AP4: Festlegen und Kategorisierung von Datenpunkten;
- AP5: Erstellung der Datenpunktbibliotheken sowie Ausarbeitung der WS-Dokumentation (Inhalt und Auswerteempfehlungen).
Im Folgenden wird auf die einzelnen Arbeitspakete eingegangen und die Herausforderungen sowie die Kernpunkte des Weihenstephaner Standards für Brauereiprozesse aufgezeigt.
Anforderungsdefinition
Zur Anforderungsdefinition wurden zwei Masterarbeiten an den TUM-Lehrstühlen für Brau- und Getränketechnologie sowie Lebensmittelverpackungstechnik durchgeführt. Ein Online-Fragebogen ermittelte dabei zum einen die notwendigen brauereiprozesstechnischen Daten, zum anderen wurden leitfadengestützte Experteninterviews mit den teilnehmenden Projektpartnern durchgeführt. Das Projektkonsortium setzte sich aus einem Querschnitt an repräsentativen Unternehmen aus Maschinenbau, IT-Systemanbieter sowie Brauereien zusammen (s. Abb. 2). Als Ergebnis des ersten Arbeitspakets konnten bereits die Systemgrenzen des neuen Standards festgelegt sowie die Anforderungen an die Schnittstelle (auch an über- und untergeordnete Systeme) in der Brauerei definiert werden. Zudem konnten – neben einem ersten Querschnitt aus benötigten Daten aus der Brauerei – die drei Kernfunktionen von optimalen Brauerei-MES-Systemen festgelegt werden:
- das Qualitätswesen (inkl. Chargenrückverfolgung);
- die Leistungsanalyse;
- das Produktionsmanagement.
Brauereirelevante MES-Funktionalitäten
Die anschließende Beschreibung der MES-Funktionalitäten wurde mithilfe von zahlreichen bi-direktionalen Gesprächen mit den Projektpartnern weiter ausgearbeitet. Durch die Modellierung der Funktionen in einem Modellierungseditor (Modellierung der Anlagen, Prozesse sowie MES-Funktionen) konnten bereits Teile der dafür benötigten Datenpunkte abgeleitet werden.
Die größte Herausforderung bestand dabei in der Abbildung der zur diskreten Fertigung (Flaschenkeller – WS Pack) unterschiedlichen Produktionsweise. Anders als bei der stückweisen Produktion auf unterschiedlichen Maschinen, welche zu jedem Zeitpunkt Informationen wie Zustände, Parameter und Zählstände liefern können, finden Änderungen bei der chargenorientierten Fahrweise nur in „großen“ Zeitabständen und in Verbindung mit der ablaufenden Prozedur statt. Daher wurden die Weihenstephaner Standards für Brauereiprozesse auf der Grundlage bestehender Standardisierungen für die Produktion in Chargen (ANSI/ISA-S88) sowie der ANSI/ISA-S95 zur Integration der Unternehmens- und Betriebsleitebene entwickelt. Durch das Mapping der Brauereiprozesse mit den S-88-Standards ist eine einfache Integration gewährleistet, auch in bestehende Systeme. Die lückenlose Chargenrückverfolgung wird in WS Brew durch die Abbildung der Transfers zwischen den einzelnen Produktionseinrichtungen (Units) gewährleistet. Wird ein Transfer durch das Prozessleitsystem angestoßen bzw. abgeschlossen, muss ein bestimmter Datensatz gefüllt und an das übergeordnete MES übermittelt werden. Dabei kann das Sudhaus einerseits als virtuelle Unit, anderseits aber auch einzeln in jedes Gefäß unterteilt abgebildet werden (vgl. Abb. 3).
Die Übertragung der Daten soll, genau wie in Zukunft auch bei den bestehenden Weihenstephaner Standards, über OPC UA erfolgen. Hierfür wurde eine Arbeitsgruppe gebildet, die momentan eine sogenannte „Companion Specification“ in Zusammenarbeit mit der OPC Foundation erarbeitet. Dadurch ergeben sich einige Veränderungen zum derzeitigen Kommunikationsprotokoll. Im oben genannten Fall der Chargenrückverfolgung werden die geforderten Datensätze als „Event“ ausgelöst und zusammengehörige Daten in einer gemeinsamen Liste konsistent via OPC UA übertragen.
Relevante Kennzahlen – Datenpunkte
Ausgehend von der Bestimmung von relevanten Kennzahlen zur Bewertung der Produktion in der Brauerei konnten erforderliche Datenpunkte abgeleitet werden. Diese Kennzahlen sind in der Auswerteempfehlung der WS Brew-Dokumente enthalten. Dabei wird ein erweitertes OEE-Konzept erläutert und vom VMDA definierte Kennzahlen für MES zum Teil übernommen. Das Hauptaugenmerk liegt aber auf brauereispezifischen Kennzahlen, wie zum Beispiel die Sudhausausbeute oder der Bierschwand. Neu eingeführt wurden auch sogenannte „Computed Values“. Dies sind Werte, die während des laufenden Prozesses erfasst und ausgewertet werden. Sie umfassen beispielsweise die Aufnahme von Minimal-, Maximal- und Durchschnittswerten. Eine weitere Rolle spielen Energie- und Medienverbrauchswerte, die vor allem in Verbindung mit den Units und den aktuell ablaufenden Prozeduren von Relevanz sind.
Die MES-Funktion Produktionsplanung wurde in Zusammenarbeit mit zwei der Projektpartnern im Detail erarbeitet und die erforderlichen Datenpunkte abgeleitet. Der Fokus liegt hier in der Echtzeit-Rückmeldung des Produktionsfortschritts aus der Produktion, um eventuelle Verzögerungen schnell erkennen und daraufhin gegebenenfalls entsprechend umplanen zu können. Zudem ist das Materialmanagement mit Warnmeldungen, wie geringer Bestand eines Materials, sowie Datenpunkte zur Bestimmung der Kapazität der Produktionseinrichtungen berücksichtigt worden.
Dokumentation
Alle für die Erfüllung der aufgeführten MES-Funktionen benötigen Datenpunkte wurden in den WS Brew-Unterlagen eindeutig beschrieben und kategorisiert. Die Datenpunktbibliothek kombiniert die über 200 neu definierten Datenpunkte mit bereits bestehenden WS-Datenpunkten. Diese sind in der Software WS Edit 38 verschiedenen Produktionseinrichtungen (z.B. Maischbottich) zugeordnet und bilden deren Anlagenprofil. Natürlich besteht die Möglichkeit, weitere kunden- und herstellerspezifische Datenpunkte zu definieren und diese einer Datenpunktbibliothek hinzuzufügen.
Zurückblickend ist über die gesamte Projektlaufzeit in intensiver Zusammenarbeit mit dem Konsortium, dem ein besonderer Dank gilt, eine erste Version des Weihenstephaner Standards für Brauereiprozesse entstanden. Diese muss sich nun in der Praxis beweisen. Nur durch Projekterfahrungen kann der Standard auch noch weiterentwickelt und verbessert werden, sodass für die Brauereibranche eine noch kostengünstigere, simplere und effizientere Integration von MES ermöglicht werden kann.
Die Unterlagen zu den Weihenstephaner Standards für Brauereiprozesse sowie weitere Informationen zu den WS sind auf der Website www.weihenstephaner-standards.de zu finden.
Name | Datei |
---|---|
Weihenstephaner Standards für Brauereiprozesse |
![]() |